Spinning process pdf
- PDF Development of Integrated Stub End by Spinning Process.
- PDF 6.9 Synthetic Fibers - US EPA.
- Handbook: The Ultimate Guide To Metal Spinning - wordpress.
- Sheet Metal Spinning - Manufacturing Process.
- Spinning process pdf - Strikingly.
- PDF Computer Modelling of The Lyocell Fibre Spinning Process.
- Cotton Yarn Spinning - The Basics process of Manufacturing Yarn - BYJUS.
- Sustainability in the Spinning Process | SpringerLink.
- Textile SPINNING - Texcoms Worldwide.
- Functions, Objectives and Actions of Drawing in Spinning Process.
- 2. Different Spinning S - Different Spinning Process for Man.
- Fiber spinning process pdf - ONLINE CASINO powered by Doodlekit.
- Ginning: Cotton Ginning, Process, Types, and Objectives.
- Flow Chart of Dry Spinning Process - Textile Flowchart.
PDF Development of Integrated Stub End by Spinning Process.
Spinning is the act of taking animal fibers or vegetable fibres and twisting them to form a continuous, infinitely stretching yarn suitable for weaving. Simply put, it is the process of spinning fibres into yarn by mechanical means. Here, take the cotton fibres for example to illustrate the six processes involved in spinning. The spinning process of Lyocell fibres in the air gap can be considered as a melt spinning process. For a steady-state process of melt spinning, the following equations are well known [1, 2] but should be recalled as the basis for performing the measurements and calculations discussed below: Mass continuity equation constant 4 2 =W = d x v. Production spinning route for synthetic fibres, is also used to process wool for carpet yarns. There are a number of processes common to both systems: blending of the wool types to be used; scouring of the wool to remove a range of impurities e.g. dirt and grease; carding to.
PDF 6.9 Synthetic Fibers - US EPA.
Materials used in the spinning process include non-alloyed carbon steels, heat-resistant and stainless steels, non-ferrous heavy metals and light alloys. The process is capable of forming a workpiece with a thickness of 0.5 mm to 30 mm and diameter of 10 mm - 5 m. Due to its incremental forming feature, metal spinning has some unique advantages.
Handbook: The Ultimate Guide To Metal Spinning - wordpress.
.
Sheet Metal Spinning - Manufacturing Process.
Keeping this in mind, process control and yarn quality in spinning outlines the concepts of raw material selection, control of various process parameters to optimise the process conditions, and analysis and interpretation of various types of test reports to find out the source of fault. The book is divided into thirteen chapters, each discusses. A combing machine is a one type spinning machine for spinning process of yarn which has comb to straighten the fibers and extract neps, foreign matter and short fibers. Combing machine is used to produce higher count yarn stronger , more even, more compact, finer, smother. The yarn which is produced by using combing machine is called combed.
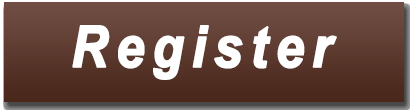
Spinning process pdf - Strikingly.
PDF Novel Plasticized Melt Spinning Process of Polyacrylonitrile Fibers. PDF Airjet Spinning of Cotton Yarns - Cotton Incorporated. Gel spinning process pdf - FREE SPINS NO DEPOSIT MOBILE CASINO. Melt Spinning , Dry spinning and Wet Spinning Method. Metal Sheet Spinning process | Sheetmetal Forming. PDF Analysis of tube spinning process.
PDF Computer Modelling of The Lyocell Fibre Spinning Process.
When the yarns are produced from the extracted fibers, that process is called Spinning. Here, in this process -. Twisting of the cotton strands together to form yarn takes place. The yarn is placed on the rings of the spinning frame and is then passed through several sets of rollers, which are rotating at a successively higher speed.
Cotton Yarn Spinning - The Basics process of Manufacturing Yarn - BYJUS.
Spinning mill into a reliable partner within the whole produc-tion chain. In addition, the detailed quality and production reports provide information on options for optimizing the preparation and spinning process. Spinners can rely on peak technological performance from ZENIT. MEETS YOUR NEEDS Fully cleared yarn to meet market demand. Reaction spinning Spandex Rayon viscose process 6.9.2.1 Melt Spinning - Melt spinning uses heat to melt the polymer to a viscosity suitable for extrusion. This type of spinning is used for polymers that are not decomposed or degraded by the temperatures necessary for extrusion. Polymer chips may be melted by a number of methods. Spinning is the process of taking textile fibers and filaments and making them into yarn. For thousands of years, people spun natural fibers into yarn by hand. Today, spinning involves many.
Sustainability in the Spinning Process | SpringerLink.
Drawing is the last third step conducted in the spinning process after blowroom, carding, combining and prior to roving and cone winding.Fibers are blended, levelled and doubled in the textile manufacturing process by drawing in spinning process.By drawing silvers from carding process are enlarged when they are made pass through rollers. This procedure conducted in spinning mills allows. PLA Processing Guide for Spinning Fibers This information is intended for use only as a guide for the manufacture of PLA fibers. Because melt spinning and downstream processing of PLA fibers is complex, an experimental approach may be required to achieve desired results. 1.0 Safety and Handling Precautions.
Textile SPINNING - Texcoms Worldwide.
Open-End Spinning The heart of the open-end process is a rotor see Exhibit 3, wherein fibers can be collected and then drawn off as a yarn. For short staple spinning, most rotors are 31 to 56 millimeters in diameter and may contain a shallow quot;Uquot; or quot;Vquot; shaped fiber alignment groove around their periphery. In open. Process Quality Control. fThe process or processes Textile spinning used in the production of single yarns or of fabrics generated directly from polymer. 1. Yarn from Staple Fiber: The formation of a yarn by a Click to edit Masterdrawing combination of subtitle style or drafting and twisting prepared strands of fibers, such as roving.
Functions, Objectives and Actions of Drawing in Spinning Process.
A Straightforward Text Summarizing All Aspects of Process ControlTextile manufacturing is one of the largest industries in the world, second only to agriculture. Spinning covers a prominent segment in textile manufacturing, and this budding industry continues to thrive and grow. Process Management in Spinning considers aspect of process management, and offers insight into the process control.. Cotton Yarn Spinning. The spinning of cotton yarn is the initial stage of textile product processing. The process of producing yarns from the extracted fibres is called spinning. In this process: The strands of cotton fibres are twisted together to form yarn. The yarn is placed on the rings of the spinning frame and is allowed to pass through.
2. Different Spinning S - Different Spinning Process for Man.
.
Fiber spinning process pdf - ONLINE CASINO powered by Doodlekit.
Objectives of air jet spinning: 1 To investigate the influence of process variables on yarn structure and yarn characteristics in air jet spinning. 2 To study the migratory behavior of fibres in air jet yarns by varying important process/machine parameters. 3 To predict the tenacity of blended air jet spun yarns by various models. 4 To. The process of spinning the cocoon by the worms takes about 1 to 2 days in the case of multivoltines and 2 to 3 days in the case of uni/bivoltine worms. It is necessary to keep the silkworm larvae undisturbed during this period, because shaking during cocoon spinning causes suspension of spinning and even breaking of the thread.
Ginning: Cotton Ginning, Process, Types, and Objectives.
The melt solidifies immediately it issues from the jets and so form filaments passes through a cooling chamber in which cold air current swept across the filaments. The spinning speed is approximately 1200 meters per minute. Melt spinning process has two huge advantages over dry spinning. Those are-. It avoids the need for a solvent recovery..
Flow Chart of Dry Spinning Process - Textile Flowchart.
Repeat. Hot spinning heats a flowformed metal tube as it spins on a lathe at high speeds while various rollers and tools shape the piece. Computers control various machine tools that adjust for everything from feed rate, coordination, location, temperature and speed. The process accurately controls the profile of the neck while delivering. PROCESS. Spinning sheet metal on the lathe is an excellent means for quickly prototyping round hollow metal forms primarily the realm of expensive sheet metal stamping machinery. A levered force is applied uniformly to the sheet metal by rotating the metal and its intended form mandrel at very high rpms, thus the sheet metal is deformed evenly without. Metal spinning, also known as spin forming or spinning or metal turning most commonly, is a metalworking process by which a disc or tube of metal is rotated at high speed and formed into an axially symmetric part. Spinning can be performed by hand or by a CNC lathe.. The metal spinning trade is one that dates back to antiquity and was a skill used in the Ancient Egyptian era.
Other content: